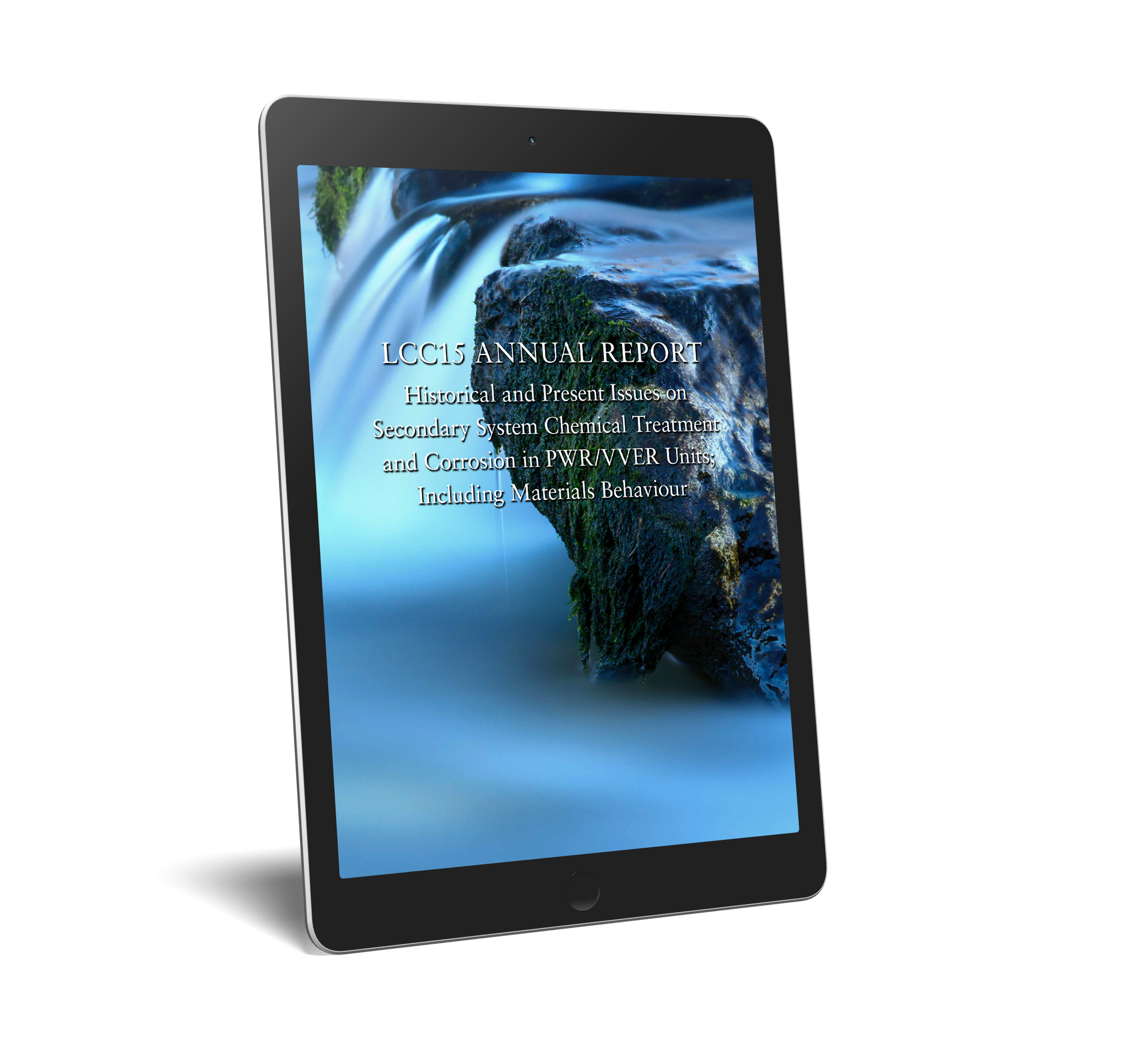
This report describes and explains the past and present issues related to secondary system chemistry and materials behaviour.
It starts with the relation between design and material evolution influence on chemistry selection, as well as guidelines for the secondary system. It also explains the behaviour of added reagents and of impurities in the secondary system. The integrity and long-term behaviour of the plant is largely considered.
The evolution of design on materials includes the condenser tubing and tightness, the steam generator blowdown flow rate and location, the tube support plate, and the very important steam generator tubing material (Alloys 600 MA, 600 TT, 800, 690 TT, and 18-10 of VVER). The link with various degradations (wastage, denting, Inter-granular Attack/Stress Corrosion Cracking) is explained.
The reagent selection is detailed, based on design and material evolution and encountered degradations and new issues. The advantages and inconveniences of H-AVT and various amines treatments are explained. The optimum hydrazine concentration depending on various parameters is described. The distribution of the reagent within the secondary system is covered as well as the behaviour of various impurities (Na, Cl, organic acids, etc.).
The important issue of corrosion products generation, deposition and elimination is reminded with the selection of adequate treatment, while other remedies are briefly listed (dispersant addition, film forming amine, chemical cleaning, sludge lancing etc.).
Another issue on liquid and solid wastes, as well as sometimes associated operating cost, is explained. This covers the best selection of reagents and purification system (limitation of the use of condensate polishing plant, operating mode of steam generator blowdown).
It finally clarifies the potential influence of lead on various steam generator tubing materials, and different chemical environments.